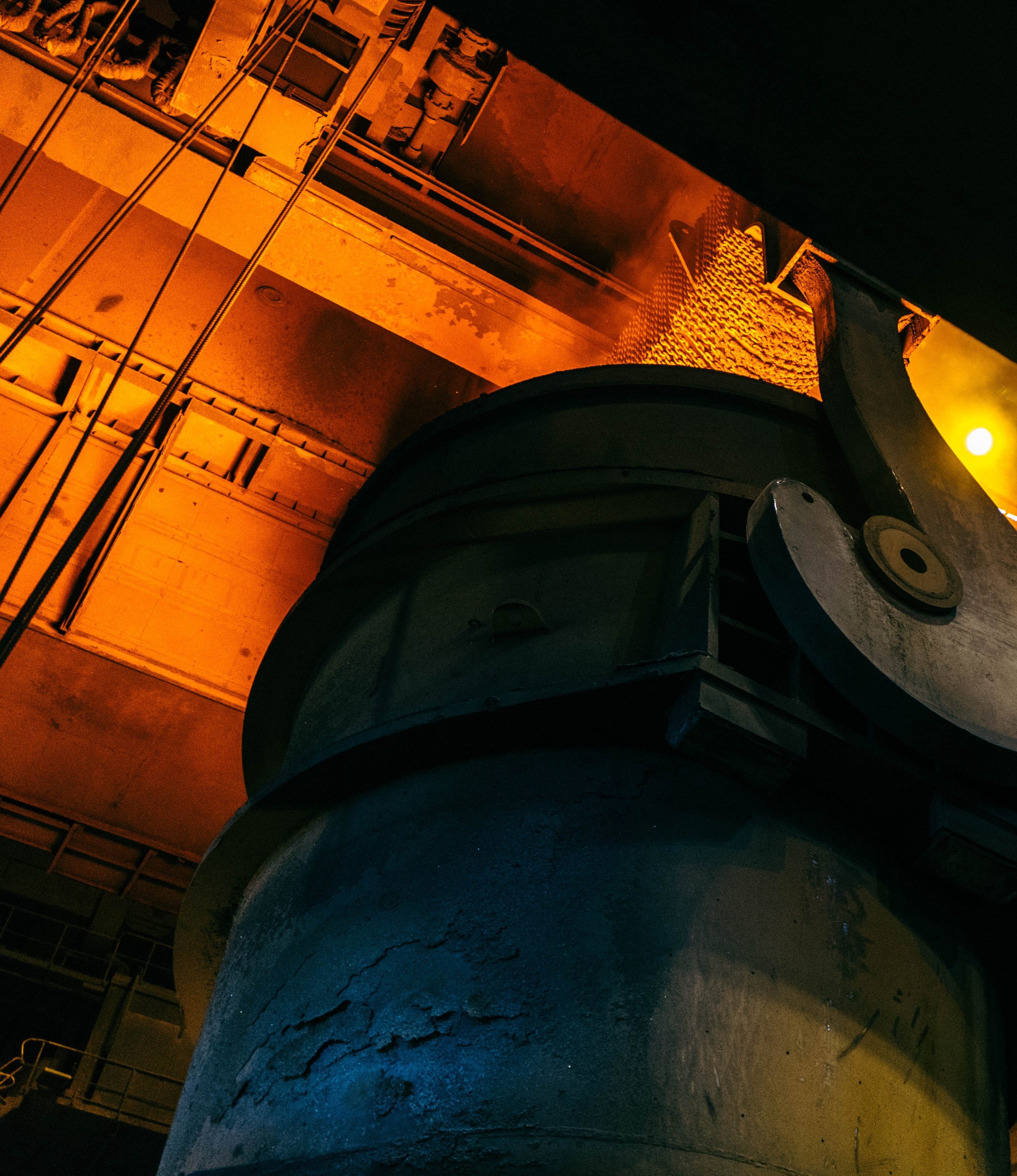
Shaping the Future of Steel Production Training: Tata Steel's Pioneering Use of VR with Steel Sim VR and Varjo
Tata Steel, in collaboration with Steel Sim VR and Varjo, is paving the way for a safer, more efficient future for industrial training. Their state-of-the-art virtual reality simulator for crane operator training not only improves safety and reduces costs but also catalyzes industry-wide digital transformation.
Benefits of VR in Steel Production Training:
- Enhanced Safety: Offering a safe platform for learning, even for high-risk scenarios and uncommon automation fails
- Cost-Effectiveness: One-time investment yielding long-term benefits and significantly reducing training costs
- Time Efficiency: Operators can begin hands-on training from day one, eliminating the need for continuous mentorship and saving countless hours of training
- Quick Evaluation: Expediting the process of assessing a prospective operator’s suitability for the job
- Attracting New Employees: The use of cutting-edge technology in training can be a compelling draw for potential hires
Navigating the High-Risk Landscape of Steel Production
Steel production is inherently associated with a multitude of high-risk operations and scenarios. The production process, which involves melting metal at extremely high temperatures, can be hazardous, as workers are often exposed to extreme heat, molten metal, and heavy vessels and machinery. Any misstep or spillage during this operation can have catastrophic implications.
With safety being a vital concern in the industry, Tata Steel has been pioneering in automating many aspects of their steel plants’ operations. Yet, as is always the case with machinery, failures can occur, necessitating manual override of the automation. This poses a significant challenge as operators are often inexperienced in manual procedures, given the typically reliable nature of the automation.
Due to the complexity and inherent risks of production processes, it’s vital that crane operators undergo comprehensive training that equips them with hands-on experience to swiftly react in any scenarios they may come across. To evolve from the traditional and often time-consuming apprentice-style route of training new drivers, transitioning into a virtual environment was the next logical step for Tata Steel’s IJmuiden Works. When securing funding for their digital transformation presented a challenge, the steelworks took matters into their own hands – and the solution turned out to be closer than they could have imagined.
A Partnership Driving Efficiency and Safety in Crane Operator Training
As luck would have it, Tata Steel’s IJmuiden Works discovered the potential of a local solutions provider, Steel Sim VR, situated just ten kilometers away from their premises. With a proven track record, having successfully constructed a crane simulator for Tata Steel at Port Talbot, UK, and ArcelorMittal Gent and Bremen, Steel Sim VR emerged as the ideal partner for spearheading the shift towards virtual training. Capitalizing on this opportunity, Tata Steel’s IJmuiden Works entered a collaboration with Steel Sim VR, leading to the creation of an innovative digital model of their loading crane.
Established in 2018, Steel Sim VR was born from a one-off project to develop a lean and efficient VR-based training tool for the steel industry. The company aims to revolutionize crane operator training by replacing the dangerous, costly, and time-consuming traditional training methods with safer and more streamlined virtual simulations. “We were one of the first to incorporate virtual reality into this type of simulation training,” explains Jan Luc Zandjans, Co-Founder of Steel Sim VR.
The exceptional clarity and comfort of the Varjo headset enabled users to undertake training for extended periods comfortably, making it the perfect choice as the cornerstone for their training solutions. “Upon testing Varjo, we found it to be the best option available, so it was an easy decision to choose the most advanced headset for training personnel. We were amazed, as nothing else we had seen could compare to it,” Zandjans says.
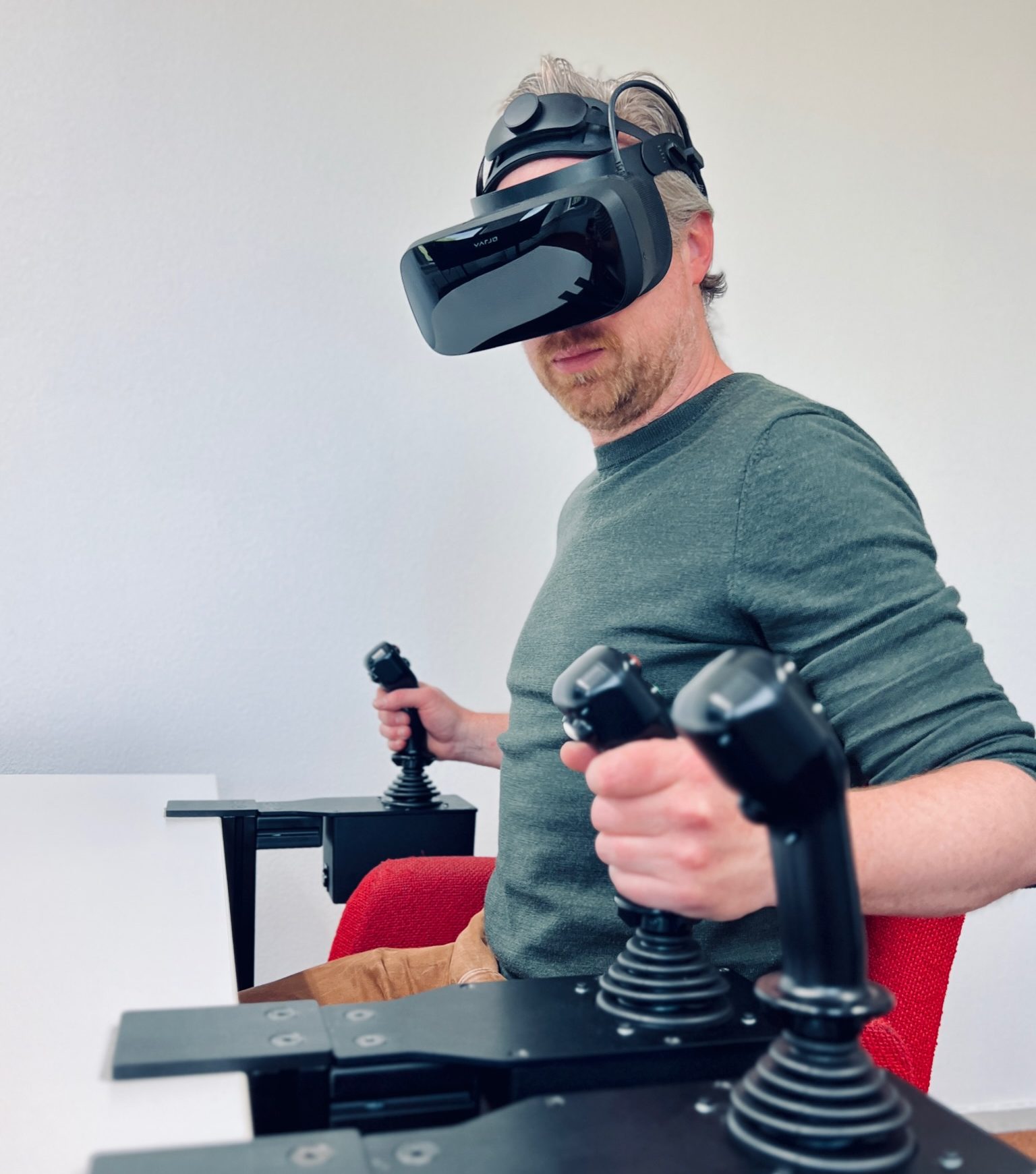
“The virtual reality simulation is an exact copy of what happens in real life. The simulation feels just like operating an actual crane.”
Hans Pronk - Steel Making Operational Expert, Tata Steel Europe
Inside Tata Steel's Innovative VR Simulator
The collaboration between Tata Steel and Steel Sim VR paved the way for a state-of-the-art VR-based simulator designed to emulate training in a real-life crane cabin. Thanks to the Varjo Aero headset, everything inside the virtual cabin is crystal clear and easy to see, including details such as various screens for tasks, text and number displays, cabin buttons and joysticks. “With Varjo, we were able to create a lifelike cabin for our training simulators, which truly enhances the overall training experience,” says Zandjans.
Once the VR simulator is fully operational at Tata Steel’s IJmuiden Works, the training program is divided into two categories: one for newcomers and the other for experienced operators. The novice operators will receive basic training, while the more seasoned ones will go through a refresher course, and both groups will be trained in handling special emergency incidents, such as automation failures or breakouts. The simulation mimics the actual crane movement precisely, helping operators gain invaluable muscle memory for when such incidents occur.
“The virtual reality simulation is an exact copy of what happens in real life. Once the headset is on, you feel as though you’re actually inside the steel factory,” says Hans Pronk, Steel Making Operational Expert at Tata Steel Europe. “The feedback from our crane operators, particularly those with extensive experience, has been overwhelmingly positive.”
Another central feature of the solution is its innovative data dashboard tracking metrics of the trainee’s performance. This tool breaks down scenarios into specific tasks and goals, while recording a trainee’s ‘flight path’ to provide insightful feedback on their movements. Using a variety of data points, operators can integrate this data with a reporting system to analyze trends and identify problematic areas. For example, the data dashboard can answer queries like ‘Which scenario results in the most collisions?’.
“There's no comparison to the safety offered by high-quality simulator training.”
Jan Luc Zandjans, Co-Founder of Steel Sim VR - Co-Founder, Steel Sim VR
Training Capabilities Beyond Comparison
The benefits of the VR solution are manifold. Firstly, the simulator offers an environment for practicing disaster scenarios, a training module previously lacking in the training repertoire across the industry. With the simulator, operators can practice situations they couldn’t safely prepare for in a real-life setting.
Furthermore, simulator training is multiple times more cost-effective and efficient compared to traditional methods. It allows an operator to start training independently from day one, saving time and money compared to traditional crane training, where a mentor or an experienced crane driver needs to be present with a less experienced one. “After several hours of training on the simulator, an operator is already prepared to work on the actual crane with a colleague. Consequently, we anticipate that this system will lead to significant reductions in training time,” says Tata Steel’s expert Hans Pronk.
One of the benefits of this technology is its flexibility. The initial investment is made once, but the benefits continue year after year. “You can easily switch to another application or environment without making any significant investment in hardware; the only required investment is in software,” Pronk explains.
Propelling the Industry into the Future
Tata Steel’s leap into VR signaled the company’s readiness to embrace future innovation, proving that the steel industry was no longer a stranger to digital transformation. Advancements in recent technology have evolved immersive solutions into a new model of cost-effectiveness, paving the way for their widespread adoption across the industry. “We now have all the necessary hardware and software to build top-quality simulators at competitive prices,” says Zandjans. “This development has made the choice between traditional training and simulator training much easier for our clients.”
Steel Sim VR sees a strong future for immersive training solutions in the steel industry, similar to the extensive adoption seen in the aviation field. “Without a doubt, training simulators are set to become the new standard for training personnel, especially in tasks involving heavy machinery and hazardous environments”, says Zandjans. “I anticipate that within the next five years, simulators will be the standard training method in the industry.”
Dive into the possibilities that VR and XR technology can bring to training and simulation: