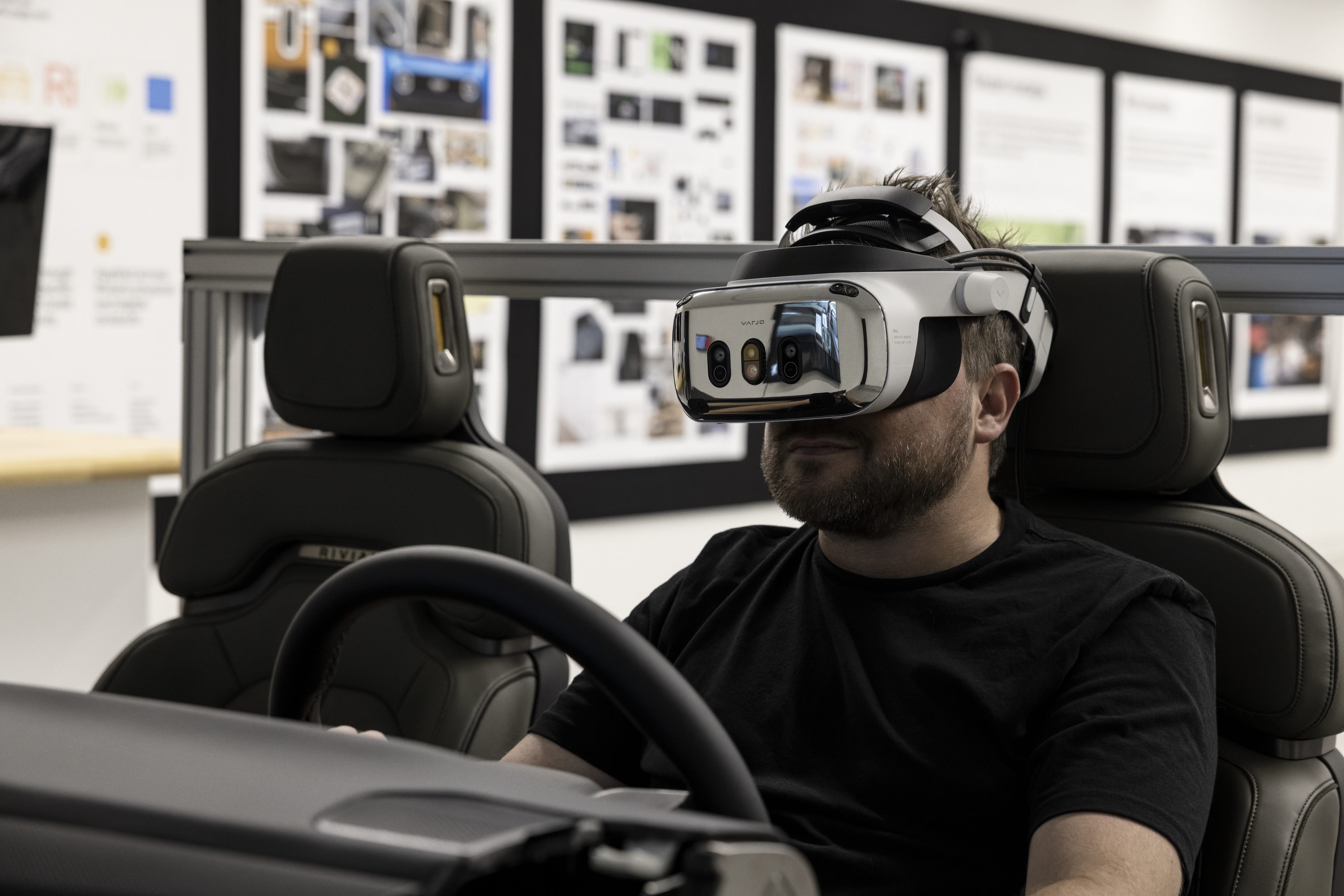
How Rivian Achieved a Faster Design Process with VR and Autodesk
Discover how Rivian, the pioneering electric vehicle manufacturer, is shifting gears towards a greener future by harnessing the power of cutting-edge virtual reality and Autodesk software. Their innovative approach is not only speeding up the design process but also drastically cutting down on emissions, waste, and costs.
Rivian is an electric vehicle company founded in the United States in 2009 that manufactures EVs such as pickups, SUVs and delivery vans. Rivian constantly aims to push the industry and technology further, and environmental considerations are extremely important to them.
As part of their commitment to the environment, Rivian has adopted a goal of net zero emissions by 2040. This also means they want to achieve a more sustainable raw material supply and consumption and want to minimize waste at all stages of the process.
Challenge: How to achieve faster, more sustainable processes
Rivian has operations across the globe, and their US teams are dispersed across multiple states. Much of the design takes place in different parts of California, test tracks are in Arizona, manufacturing in Illinois, and many other functions in Michigan. One major reason for this is the availability of talent.
People specialized in different parts of the automotive value chain tend to be located in different places. This also means that multifunctional teams across locations need to collaborate frequently. In order to avoid unnecessary travel time, expenses and emissions, Rivian wanted to achieve better ways for these teams, such as engineering and design, to collaborate remotely.
Another major challenge for them was reducing the raw materials required during the car manufacturing lifecycle. While building the cars themselves requires the biggest amount of resources, the needs for physical materials start much earlier in the design process.
Traditional vehicle design workflows involve building physical mockups that require thousands of pounds of raw materials, such as clay and wood, before the design for a vehicle model is finalized. They also require people to be physically present in the same space to review the design and develop a shared understanding – adding considerable travel time for several people and producing a lot of emissions over time.
To solve these problems, Rivian needed to leverage the latest technologies and software available. This led the team to collaborate closely with Autodesk, and ultimately resulted in them fully embracing virtual and mixed reality technologies.
Solution: Extensive virtual and mixed reality programs
Trevor Greene, Lead Visualization Design at Rivian, kicked off the company’s VR initiative in 2016, and their team has been able to achieve a lot since then. In fact, every employee at Rivian has now used virtual reality, regardless of the department they are in.
Rivian was able to do this thanks to Autodesk VRED, software that is absolutely crucial for the automotive industry. It fully supports virtual and mixed reality, so the teams at Rivian have been able to transition an increasingly bigger portion of their design work into the virtual world. With the addition of Varjo headsets, they are also able to take advantage of lifelike visual quality and color reproduction, so digital models look just like their real-world counterparts, a crucial requirement for doing more detailed design work in a virtual environment.
Better collaboration through virtual reality
According to Greene, the implementation of VR and XR technology with Autodesk helped Rivian overcome the geographical barriers of dispersed operations. People in different functions have been able to develop a shared understanding, and more importantly do so at a much earlier stage in the process. Nowadays, multifunctional teams collaborate using extended reality technologies throughout the entire lifecycle of creating a vehicle model.
This has meant faster iteration and a reduced need to go back to earlier stages in the design process, as critical inputs can be provided and potential issues corrected earlier than before. It has also enabled Rivian to align clay modeling with the use of digital models, where everything can be changed in real time, with zero raw materials being consumed.
With mixed reality, Rivian is able to combine digital and physical at a much deeper level than before. It enables them to better adapt user experiences and solve design challenges earlier. With lifelike and lifesize digital models that have reflections and textures accurately matching the real world, it is easier to answer questions such as is the steering wheel in the right position, could screens cause glare, is the seat positioned correctly and so on.
Results: Major cost savings and faster iterations
Leveraging Autodesk and immersive technology has been extremely beneficial for Rivian. The biggest benefits have been cost, time and material savings, improved sustainability, faster iteration speed, and better end-user experience.
XR has complemented the continued development of clay modeling. It typically costs around 5,000 dollars and takes 325 pounds (~150kg) of materials to create one clay model. The total materials needed to achieve the final design include more than 32 tons of raw materials, which has a major environmental footprint. A single design review done with a clay model takes about one work week and the team needs to be physically colocated. The same process can be done in VR within an hour, allows for remote participants, and is available on-demand at any time. As Rivian has embraced virtual and mixed reality, the total cost savings just from the reduced need for materials and physical mockups has been a million dollars per vehicle program.
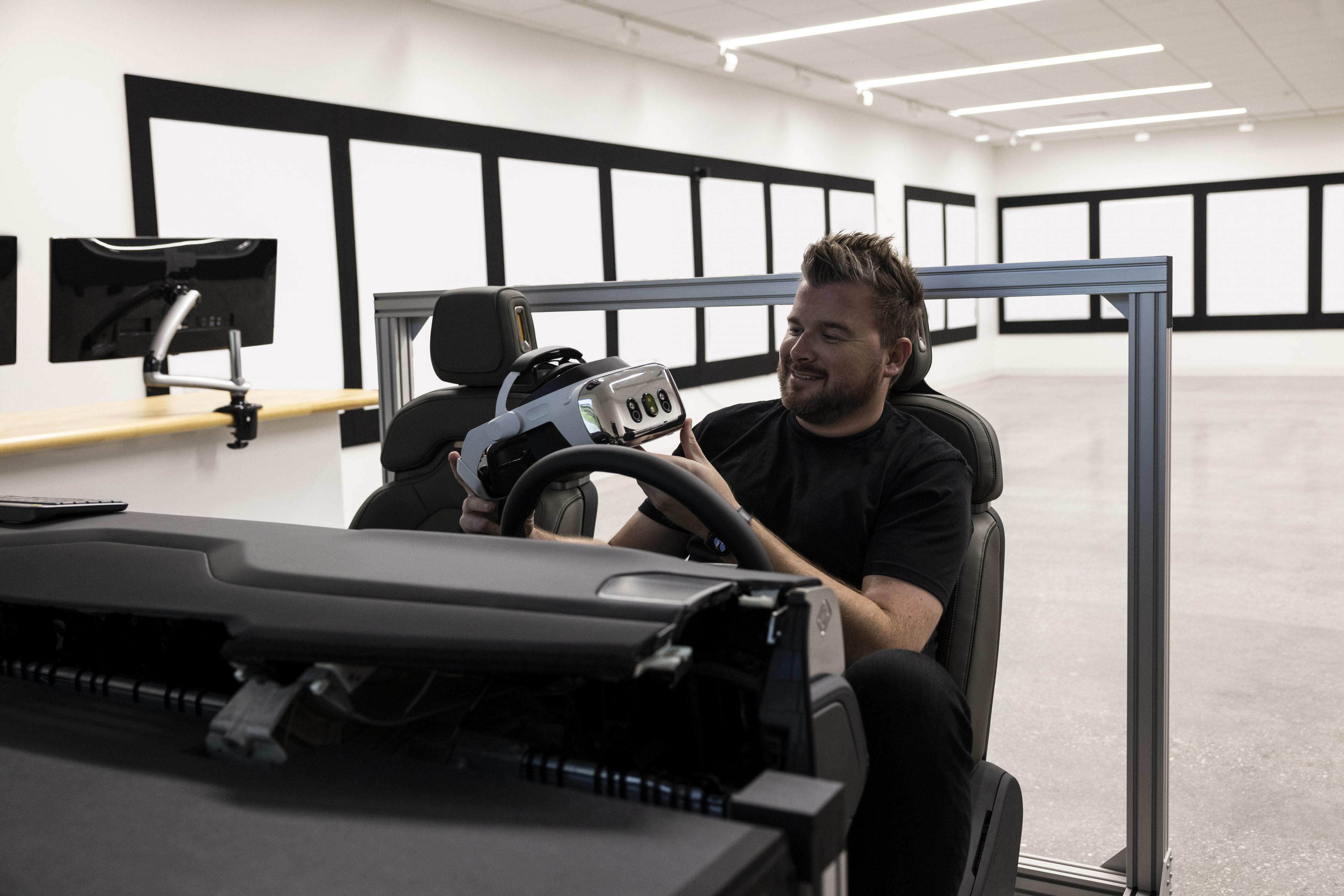
“At Rivian, design time is of the essence. Together with VRED, Varjo has taken a lot of time and money out of the process and lets us iterate and integrate more quickly than ever before.”
Trevor Greene - Lead Visualization Design at Rivian Automotive
A more sustainable design process
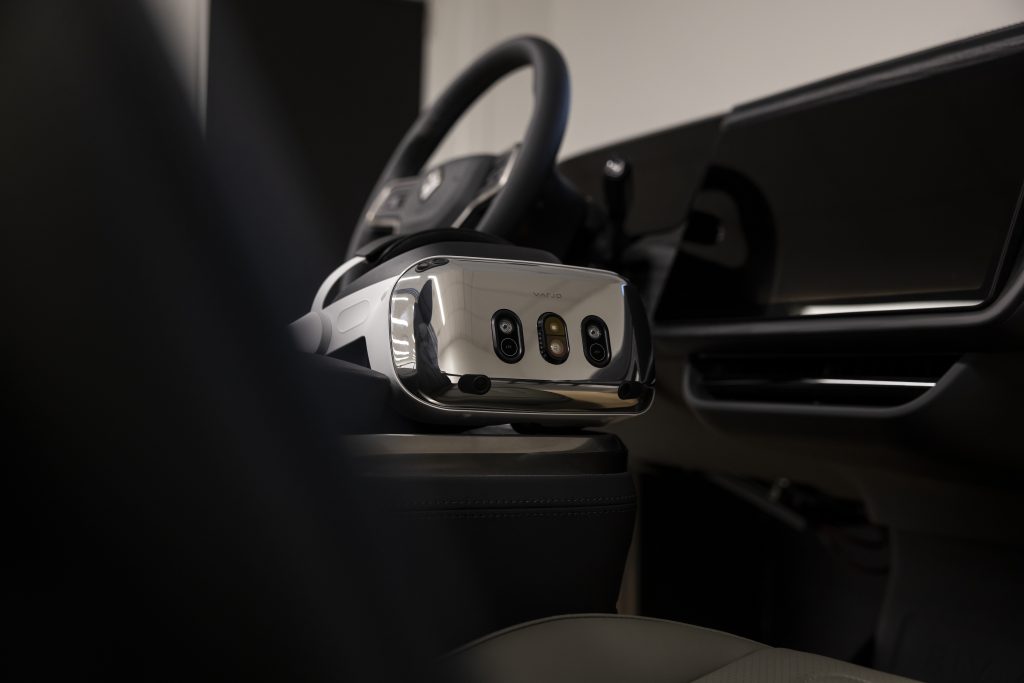
Mixed reality technology has also helped speed up the design iteration cycle, and the team is now able to create 2-3 times the amount of iterations in the same amount of time they were before. This helps the team build better cars and quickly get answers to practical questions such as does a door panel feel high, or are the driver’s seat and steering wheel placed at a good height.
Trevor Greene also emphasizes that the benefits compound over time. No car company has just one vehicle program at a time: there are always multiple new models in the works for the future, and the processes continue for years. Over time, the savings and efficiencies achieved with mixed reality accumulate to have truly meaningful scale, and also lead to a much more sustainable design process.
“We can make changes and apply a whole range of new materials and know exactly what the final product will be like. Varjo helps keep Rivian on the path of moving the industry forward,” Greene says.